Additive manufacturing of Nickel based superalloys
Nickel based superalloys have excellent high temperature strength because of which they are very commonly used in aerospace applications like turbines. To be able to effectively use melt-fusion based processes to fabricate superalloy components, it is important to understand the microstructure and mechanical property evolution through all the steps of these processes. In this project, we do that using advanced microscopy and characterization techniques.
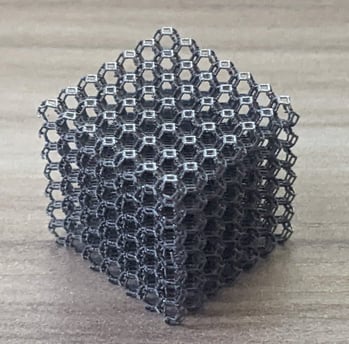
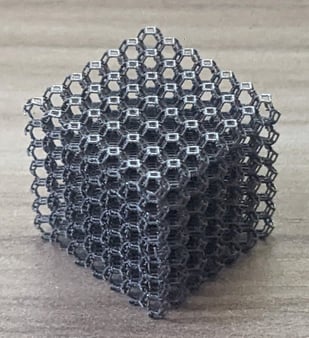
Microstructure of a single track
EBSD micrograph of a single track shows grains growing from the edge of the melt pool.
Extremely fast cooling rate during solidification pushes out high melting point elements to form dendritic laves phases
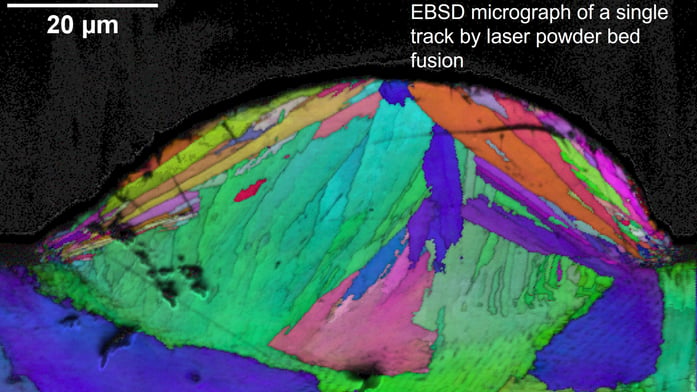
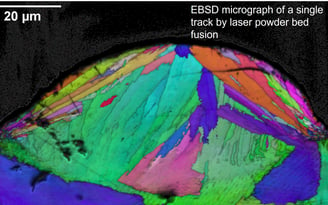
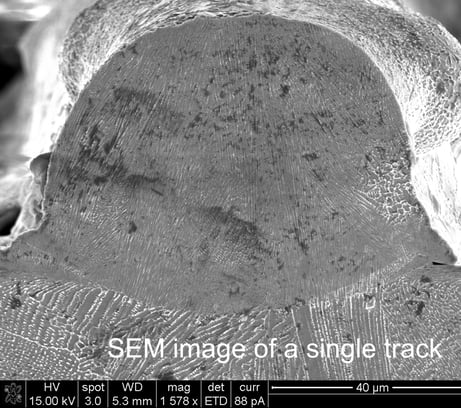
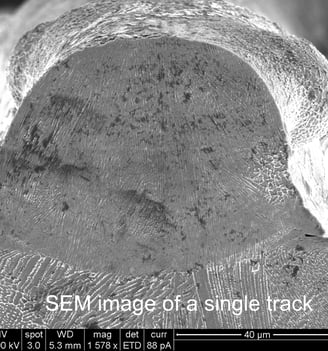
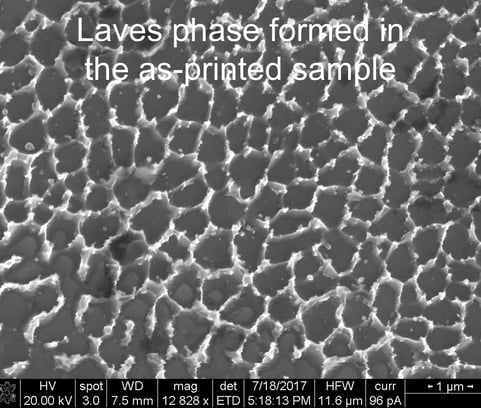
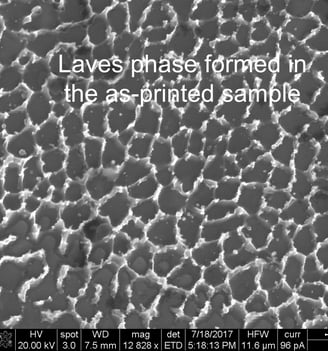
Microstructure during heat-treatment steps
Typical epitaxial grain growth is observed in the as-printed condition due to temperature gradient experienced during the powder bed fusion process.
Some recrystallization can be seen after full HT
Full recrystallization is apparent after Hot Isostatic Pressing (HIP) treatment
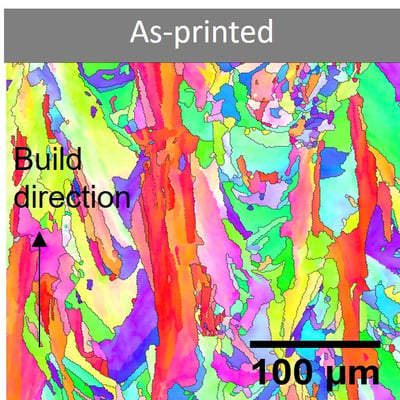
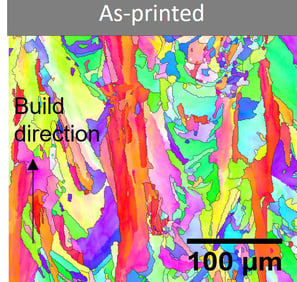
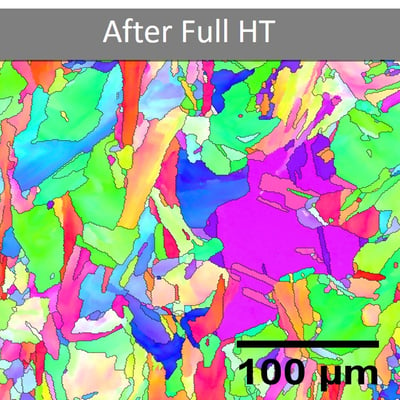
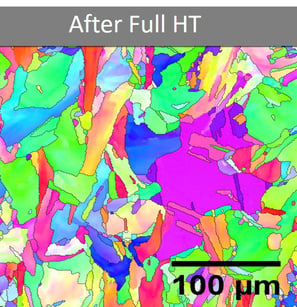
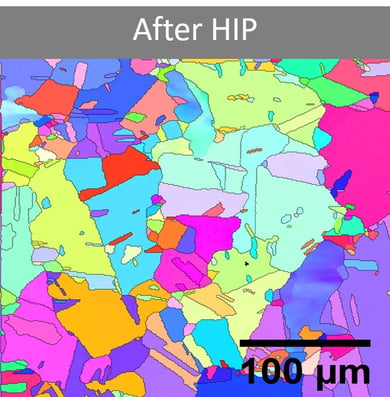
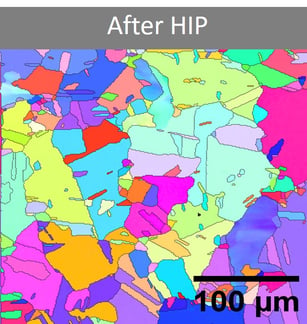
In-situ heat treatment with TEM
It is the precipitates in Nickel based superalloys that impart them with good high temperature properties. To observe the genesis of these precipitates and their growth in the early stages, we performed in-situ heat-treatment in TEM.
γ’ precipitates start forming at 950 °C
Coalescence of precipitates (shown in red) in the initial part of the in-situ heat treatment results in rapid growth in precipitate size.
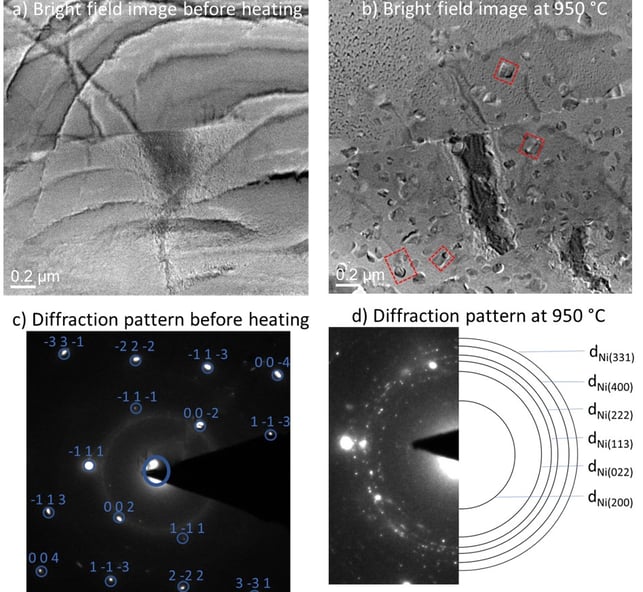
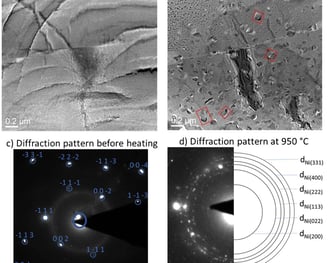